Micro-Beam designs electronic brushless motor drives, including power electronics from few milli-watts up to 10kW. Our electronic drives are usually controlled by embedded software and developed using one of the following platforms:
- DSP (Digital Signal Processor) embedded controllers from Texas (TMS320x280x, TMS320x240x family, TMS320x24x, Piccolo family)
- DSP embedded controllers from ST electronic (Cortex M0 to M4)
- 8XC196MC, 8XC196MD, and 8XC196MH embedded microcontrollers combined with analog electronic circuits such as an MSP430 or a PIC.
Micro-Beam can also support many other platform that would depend on the system requirements and the needs of the customer. For high volume production, cost considerations may suggest that integrated circuits be developed. Microbeam is skilled in motor drives using FPGA digital logic combined with analog electronic circuits that can be transferred to an integrated circuit designer to provide the customer with a low IC count, low cost solution. The electronic drive can be delivered as a standalone PCB board or schematics to be integrated into the customer's design, and may be implemented to control up to 2 brushless motors with additional DC motors and/or stepper motors, as well as other logic needed for a complete system. The embedded software can be designed to interface with the customer applications using RS232, USB, CAN, or SPI. Futher, we can add custom interfaces consisting of display screens, touch screens, buttons, potentiometers, etc. to provide a complete stand-alone product.
Depending on your needs and requirements, Micro-Beam will offer a sensorless controller or a solution based on sensors.
Sensorless
Micro-Beam develops Sensorless Brushless DC Motor Controllers. Such controllers have the following advantages:
- Closed loop motor control optimizes system efficiency.
- No sensors allows motor miniaturization.
- No sensors reduces motor cost.
- Wire count is reduced from 8 to 3 (the 3 wires for the 3 motor phases remain, but the 5 wires for the typical Hall sensors are removed).
- System reliability is increased, especially for solutions that might include autoclaving such as those employed in medical applications.
Applications needing speed and or torque control while the motor is rotating and have limited load at startup are espescially well adapted for a sensorless drive.
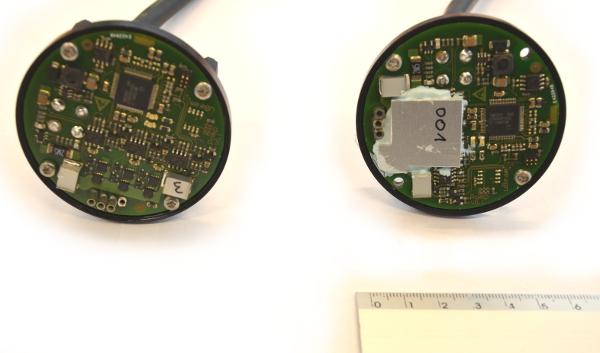
Sensorless Motor driver
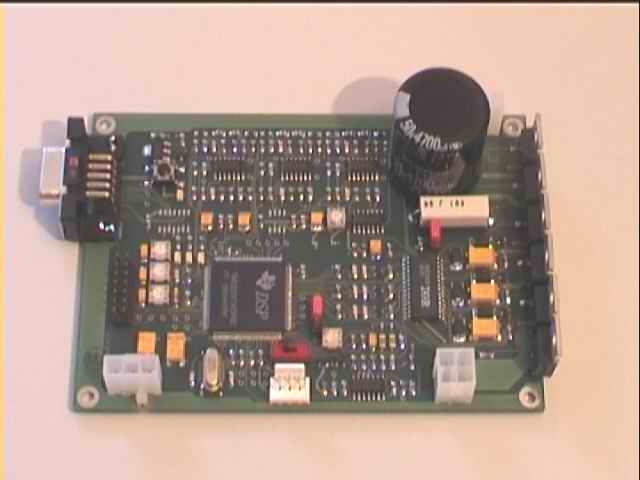
Sensorless Motor driver for speeds up to 80'000 rpm
Micro-Beam is constantly improving its sensorless technologies, extending the performances of its algorithms and reducing the hardware needed on the controllers PCB.
Last technologies allow driving motors at very low speeds or even position control with full torque. Our technologies can be applied on slotted and slotless motors, and no modification is required on the motor.
The absolut position is known on 1 turn or on several turns. This allows for example the following functions to be done:
Tapping including:
- torque limitation
- precise go and back mouvement, for example 1 turn forward and 1/2 turn backward
- auto-reverse when maximal torque is reached
- auto-review when end of hole is detected (based on position measurement)
Shaving:
- oscillating mouvement of the shaver
Linear actuators:
- allows driving linear actuators without need of position sensor
- force limitation
- failure detection if mouvement can not be done
- auto slow-down when approching the end
- reduction of number of sensors (doors for example)
With sensors
Depending on the application, using sensors might be a better choice. Micro-Beam can interface different kind of sensors and help you to choose the best option.
All manner of sensors to detect rotor parameters can be supported including but not limited to the following:
- Hall Effect sensors
- Digital Encoders
- Tachometers
- Accelerometers
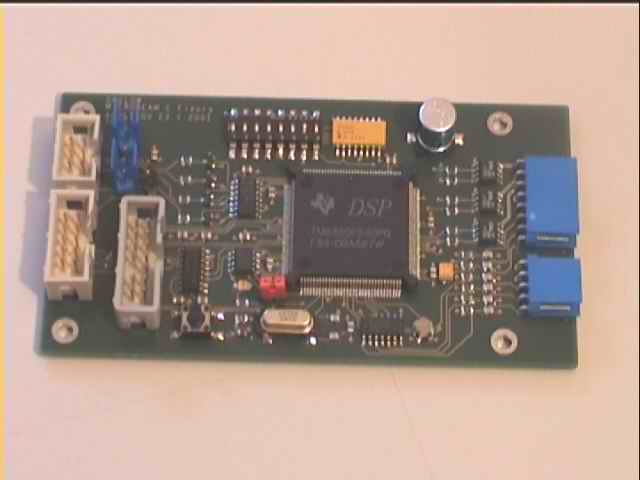
In order to provide maximum motor drive efficiency Micro-Beam can provide a solution that controls the commutation of the motor, not only based on feedbacks from position sensors but by also including motor speed as a means to optimize the drive commutation angle. For a low cost open loop solution, the electrical frequency of the supply voltage may be varied with the drive electronics. In this scenerio the load angle will change as a function of the required torque. As stated, this is a low cost solution but can be charecterized by poor efficiency compared to a close loop solution.